core Rare Metals would like to break ground on its Strategic Metals Complex (SMC) sometime this year. In about two years, the facility could be cranking out rare earth oxides, materials prized for their special properties of magnetism, luminescence, and strength.
Currently, about 80 percent of rare earths imported to the United States come from China, according to the US Geological Survey. Therefore, the Biden administration zeroed in on a domestic supply chain as part of its climate and technology policy. Ucore’s business plan is in lockstep with that national strategy.
“Ucore has a very definitive vision and plan for an independent and comprehensive North American rare earth element supply chain,” Ucore Chairman and CEO Pat Ryan says. “To accomplish this, the fundamental component is the ability to have—first and foremost—operating commercial-scale rare earth separation plants. The ability to separate rare earth elements into oxides does not exist in North America today and is, therefore, the central objective of Ucore.”
The “rarity” arises from two attributes, one physical and one economic. First, the properties of the elements prevent them from clumping in commercial quantities, and they are difficult to chemically separate from ore. Second, the overwhelming bulk of rare earth oxides are produced by China.
“That production of individual oxides, that’s where the margin is… that’s where all the money is,” Ryan says. “You’ve got to have that centerpiece, that midmarket, in order to take on the challenge of beating the stranglehold that China has and the upper hand they have over North America. So that’s why we’re focused on that.”
Ryan says that a failure to secure the supply chain for REE necessary for the electrification of the automobile sector could mean that jobs tied to North America’s combustion engine plants would eventually migrate to China. The same goes for wind turbines, defense systems, smartphones, and other 21st century technology, he adds.
“If you don’t have that on home soil, you lose the jobs,” Ryan says.
“Ideally, we would be able to potentially break ground towards the end of this year,” says Ucore Vice President and COO Michael Schrider. Construction could be complete by the end of 2023. “And then begin production of individual rare earth oxides by the first half of 2024,” Schrider says.
Ucore
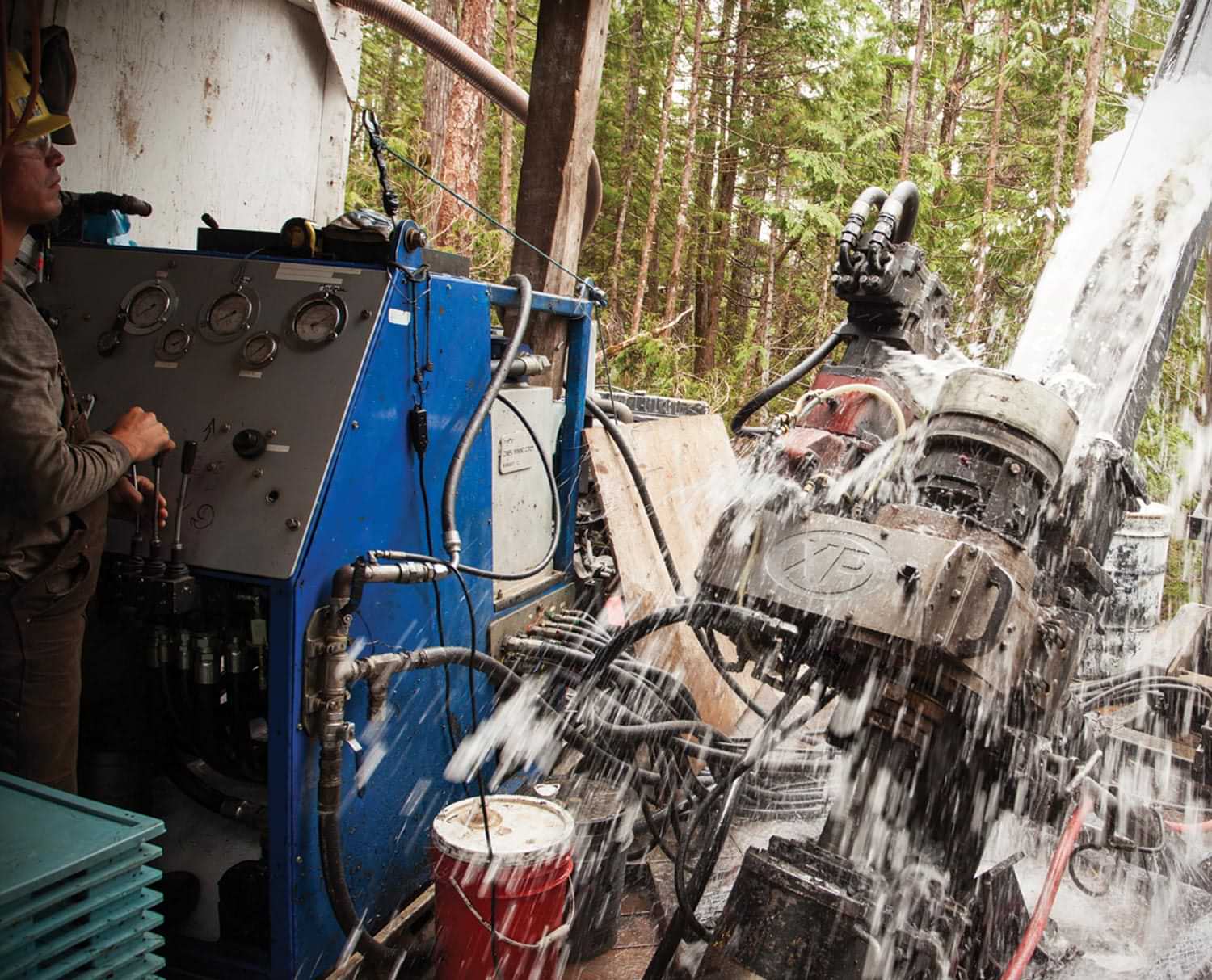
Ucore
The technology that will set the SMC apart from separators in China and elsewhere in the world is the RapidSX process, which is a huge upgrade to conventional solvent extraction methods, Ryan says. RapidSX was developed by Innovation Metals Company (IMC), which Ucore acquired as a subsidiary in 2020. In February, IMC’s top three executives announced their resignation, staying on with Ucore over the next few months to transition from “white coat science” toward commercialization.
“We are in the throes of engineering right now for the Alaska SMC facility,” Schrider says. “The IMC team is focused on the engineering development for the RapidSX portion of the plant.”
Ucore describes RapidSX as more environmentally friendly than conventional solvent extraction. The column design, which replaces traditional mixer/settler units, essentially has no moving parts, which cuts down on energy consumption, Schrider says.
“The RapidSX plant is much smaller than a conventional SX plant because it is so much more efficient than conventional SX,” Schrider says. “Because the chemistry is the same, but it’s applied in a much more efficient manner, you have much less organic chemicals than you do in a conventional SX plant.”
The main selling point of RapidSX, though, is its output speed. Conventional solvent extraction typically involves mixing “pregnant leach solution” with solvents through hundreds of mixer/settler units. With RapidSX, the time to get a solution to equilibrium, when REE are separated out, can happen in days rather than the several weeks associated with a traditional solvent extraction plant, Ryan explains.
“Then your extraction rate, which is the ability to extract a particular element from solution, is in the magnitude of ten times quicker,” Ryan says. “The chemistry is the same, but the physics and how the process works makes it all different.”
How does the process work, exactly? That’s a secret.
“You don’t want to put anything out there that’s published and noteworthy that has any hints that the Chinese could possibly get their hands on from an IP [intellectual property] standpoint,” Ryan says.
The Innovation Metals’ team decided against filing a full process patent that would describe the unique aspects of RapidSX in detail.
“It’s a bad idea because then someone can take the process patent, read exactly what’s gone on, go into their back shop, and do exactly what you explained in your process,” Ryan says. “And never tell us that’s what they’re doing, and you never know because you’d never get into their building.”
One of the reasons Ucore decided to bring Mech-Chem on board is the company’s expertise in chemical closed-loop systems and reuse of chemicals, Schrider says.
“We’re going to recycle, reclaim, and recapture virtually everything that we’re using in the plant,” Schrider says. “And that’s not necessarily done in other areas of the world.”
There are economic benefits to this system as well, as it means lower costs for shipping REE concentrates to Ketchikan and minimal costs to dispose of process chemicals, since they will be reused in the plant.
“It certainly makes sense overall from our best value position that we’re going to do what makes most sense economically,” Schrider says. “But more importantly, we’re doing what makes most sense environmentally and for the community.”
While the Ucore team is in the trenches of designing the SMC in Ketchikan, construction is already underway on a demonstration plant in Kingston, Ontario.
Originally slated to be finished in the first quarter of this year, supply chain issues for highly specialized pumps, valves, and other parts are pushing the completion date back to early in the second quarter, says Ryan.
When bringing something as unique as the RapidSX technology to market, companies typically start at a lab scale, grow it through the pilot and demonstration plant levels, and then move into the production plant.
“The reason you want to have a commercial demonstration phase is because you want to collect further data at scale,” Ryan says. “You’re collecting enough additional data to then comfortably go ahead and develop and design your commercial plant.” The data collected will be used to further optimize the construction of the commercial plant.
Another benefit is that the demonstration plant allows Ucore to test the feedstocks that will be used at the Alaska facility, adds Schrider.
“The US-allied feedstock is crucial,” Ryan says. Ucore has signed a Memorandum of Understanding that will lead to a definitive supply agreement with Vital Metals, which operates a rare earth element mine in the Northwest Territories. “Our relationship is to grow with Vital Metals,” Ryan says. “They have a very complementary growth plan to ours going forward.”
Ucore is in the process of developing two other relationships with upstream suppliers, but the negotiations were under a non-disclosure agreement at the time of writing. “All total, we’ll have at least three US-allied feedstocks that feed into the Ketchikan Strategic Metals Complex, and that’s a pretty good mix,” Ryan says.
Ucore
Another benefit is that the demonstration plant allows Ucore to test the feedstocks that will be used at the Alaska facility, adds Schrider.
“The US-allied feedstock is crucial,” Ryan says. Ucore has signed a Memorandum of Understanding that will lead to a definitive supply agreement with Vital Metals, which operates a rare earth element mine in the Northwest Territories. “Our relationship is to grow with Vital Metals,” Ryan says. “They have a very complementary growth plan to ours going forward.”
Ucore is in the process of developing two other relationships with upstream suppliers, but the negotiations were under a non-disclosure agreement at the time of writing. “All total, we’ll have at least three US-allied feedstocks that feed into the Ketchikan Strategic Metals Complex, and that’s a pretty good mix,” Ryan says.
Ucore
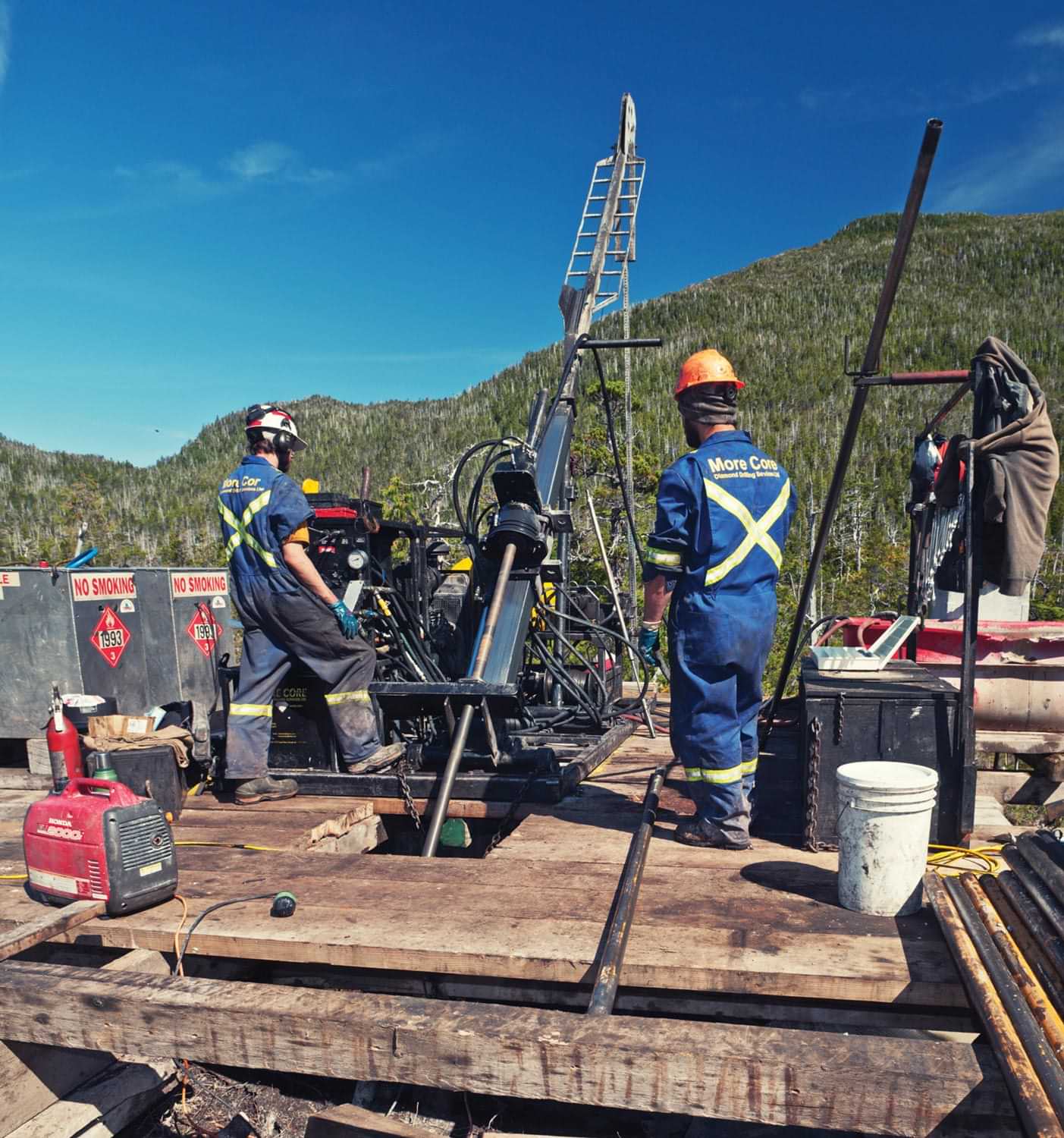
Ucore anticpates the Strategic Metals Complex will have capacity to separate 2,000 tonnes at a time, with room to grow to a 5,000-tonne plant.
“You’re better off having a smart finance plan with a smart business plan that allows you to take on customers in increments and grow with them,” Ryan says. “If you came out of the starting blocks as a 15,000- or 20,000-tonne plant… How are you going to make your way into the market?”
“That’s a good start point to take on the Chinese market,” Ryan says of the current plan. “You want to be able to build like Lego blocks. You want to be able to expand your plant effectively.”
Part of the current engineering process is gathering all the information required for the Department of Energy’s Advanced Technology Vehicles Manufacturing Loan Program’s comprehensive application, Schrider says. “Our expectation is that we will be able to submit an application sometime in the first half of 2022.” In conjunction with the application, Ucore is working on other arrangements to finance the facility.
“Some of that financing is going to come through pre-purchase supply agreements with offtake partners,” Schrider says.
Ryan explains that his background—a mechanical engineer and founder of a tier one automotive company about twenty-six years ago—puts him in a good position to understand the needs of the transportation sector and ensure Ucore is able to meet them.
“What we are doing here with this rare earth supply chain is positioning this crucial part of the mid-channel and making sure that it delivers the specifications for products that the end user, i.e. the automotive company, will ultimately want in the permanent magnet that goes into their electric motor,” Ryan says.
“This Alaska SMC that’s being designed and built is to actually address customers at the end,” he adds. “You can’t just build it and they will come. You’ve got to build it and have a sense of what the customer wants at the end of the day.”
Ryan and Schrider are keenly aware of the Made in China 2025 plan, the Communist country’s ten-year plan to transition from factory labor to more technological innovation. While Ucore’s officers recognize that the US government is making moves to control vital supply chains, they agree that the country is moving too slowly.
Ucore
Part of the current engineering process is gathering all the information required for the Department of Energy’s Advanced Technology Vehicles Manufacturing Loan Program’s comprehensive application, Schrider says. “Our expectation is that we will be able to submit an application sometime in the first half of 2022.” In conjunction with the application, Ucore is working on other arrangements to finance the facility.
“Some of that financing is going to come through pre-purchase supply agreements with offtake partners,” Schrider says.
Ryan explains that his background—a mechanical engineer and founder of a tier one automotive company about twenty-six years ago—puts him in a good position to understand the needs of the transportation sector and ensure Ucore is able to meet them.
“What we are doing here with this rare earth supply chain is positioning this crucial part of the mid-channel and making sure that it delivers the specifications for products that the end user, i.e. the automotive company, will ultimately want in the permanent magnet that goes into their electric motor,” Ryan says.
“This Alaska SMC that’s being designed and built is to actually address customers at the end,” he adds. “You can’t just build it and they will come. You’ve got to build it and have a sense of what the customer wants at the end of the day.”
Ryan and Schrider are keenly aware of the Made in China 2025 plan, the Communist country’s ten-year plan to transition from factory labor to more technological innovation. While Ucore’s officers recognize that the US government is making moves to control vital supply chains, they agree that the country is moving too slowly.
Ucore
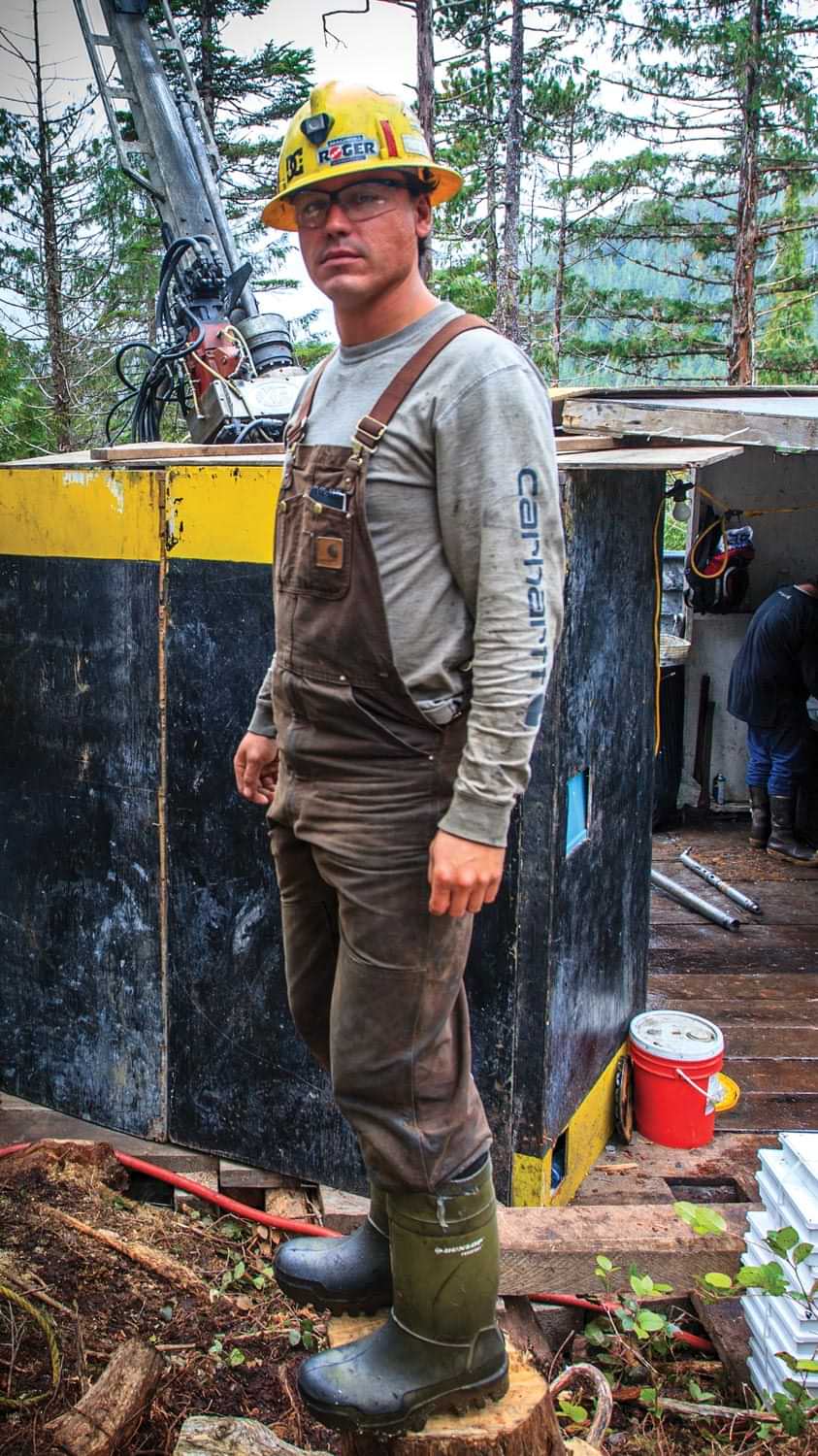
For a more preemptive defense, Ryan points to the need to have technology in place, feedstocks lined up, and customers ready to buy.
“An Alaska plant that’s up and running in 2024. That’s what you need,” Ryan says. “You need to move quick.”