Shipbuilding
Tech
onditions in arctic and sub-arctic regions are often prohibitive, which results in tight timelines for engineering projects. This also applies to the maritime industry in the state, but a recent project completed by Stillwater Marine Service (SMS) demonstrated how to tackle some of these challenges utilizing the latest engineering technology.
onditions in arctic and sub-arctic regions are often prohibitive, which results in tight timelines for engineering projects. This also applies to the maritime industry in the state, but a recent project completed by Stillwater Marine Service (SMS) demonstrated how to tackle some of these challenges utilizing the latest engineering technology.
Various considerations must be made when servicing a vessel at sea: the ice season creates a narrow window of time in which the work can be completed, accessing areas of the ship to assess them can be difficult, and existing blueprints are often outdated. Due to these factors, projects requiring fabrication typically required field fitment, costing more in time and resources. To complete this project within the client’s required timeline, SMS partnered with Eagle Harbor Engineering and Catalyst Marine Engineering.
Stillwater Marine Service
Stillwater Marine Service
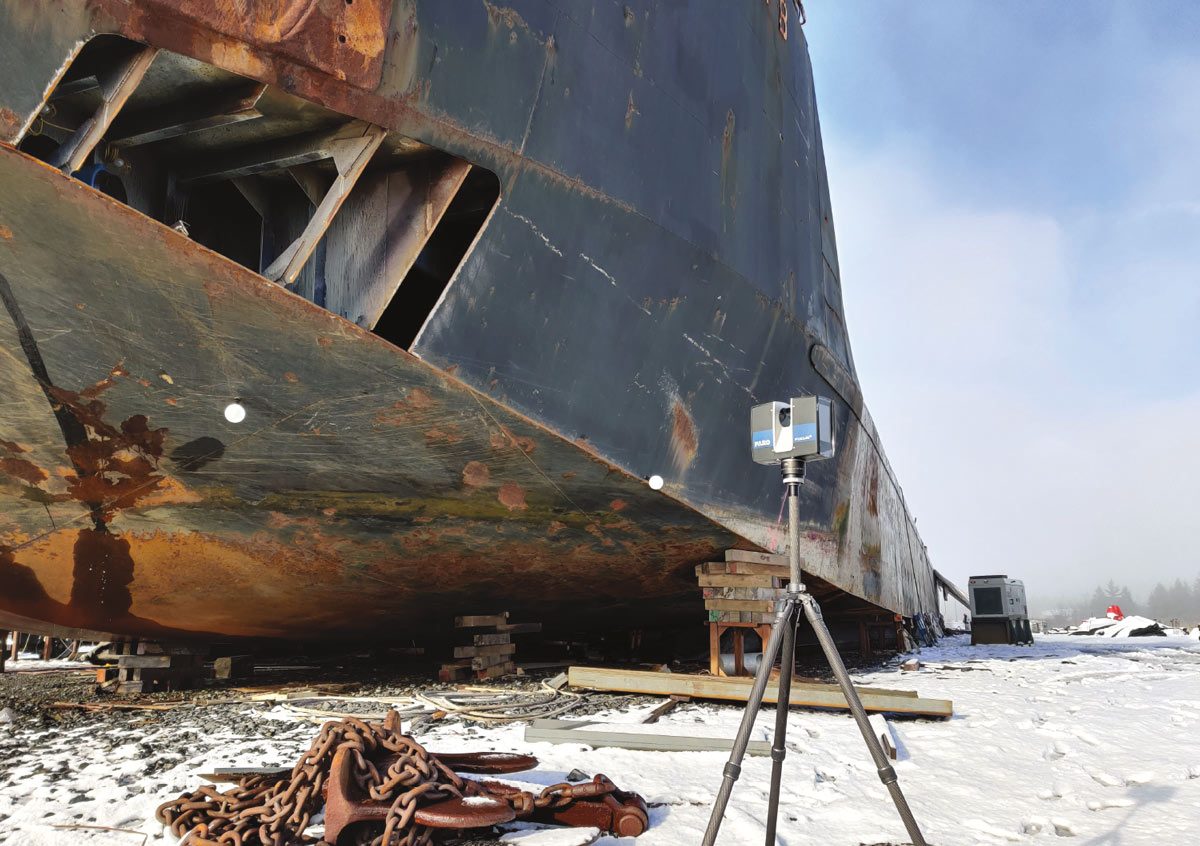
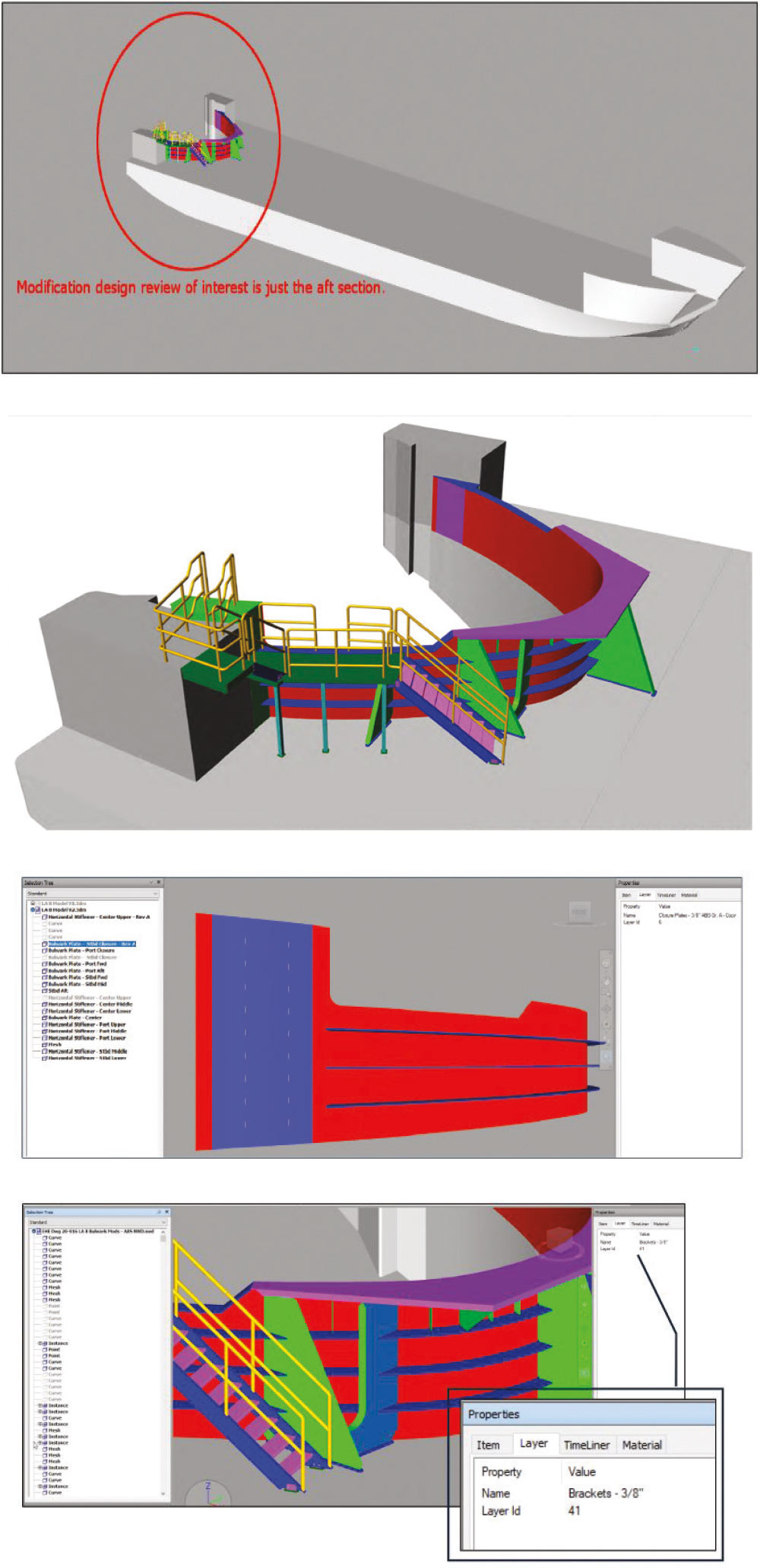
Stillwater Marine Service
“Stillwater Marine Service did an excellent job explaining how their use of technology would translate into lowered cost on execution,” says Drew McIntyre, Marine Superintendent for Brice Marine. “We were impressed with both their operational judgment and technical ability in connecting evolutions for our business model. Our final product was done faster and cheaper than I would have thought possible before working with Stillwater Marine. My only regret is missing the opportunity to have the entire barge scanned into a model during its last drydock.”
SMS licensed software to explore the data captured by the scanner in 3D space to determine the current state of the vessel in preparation for the modification. As the device can capture up to 1mm accuracy, naval architect John Van Buskirk of Eagle Harbor Engineering was able to create a workable cut-file for Catalyst Marine Engineering to use with their waterjet.
Stillwater Marine Service
Stillwater Marine Service
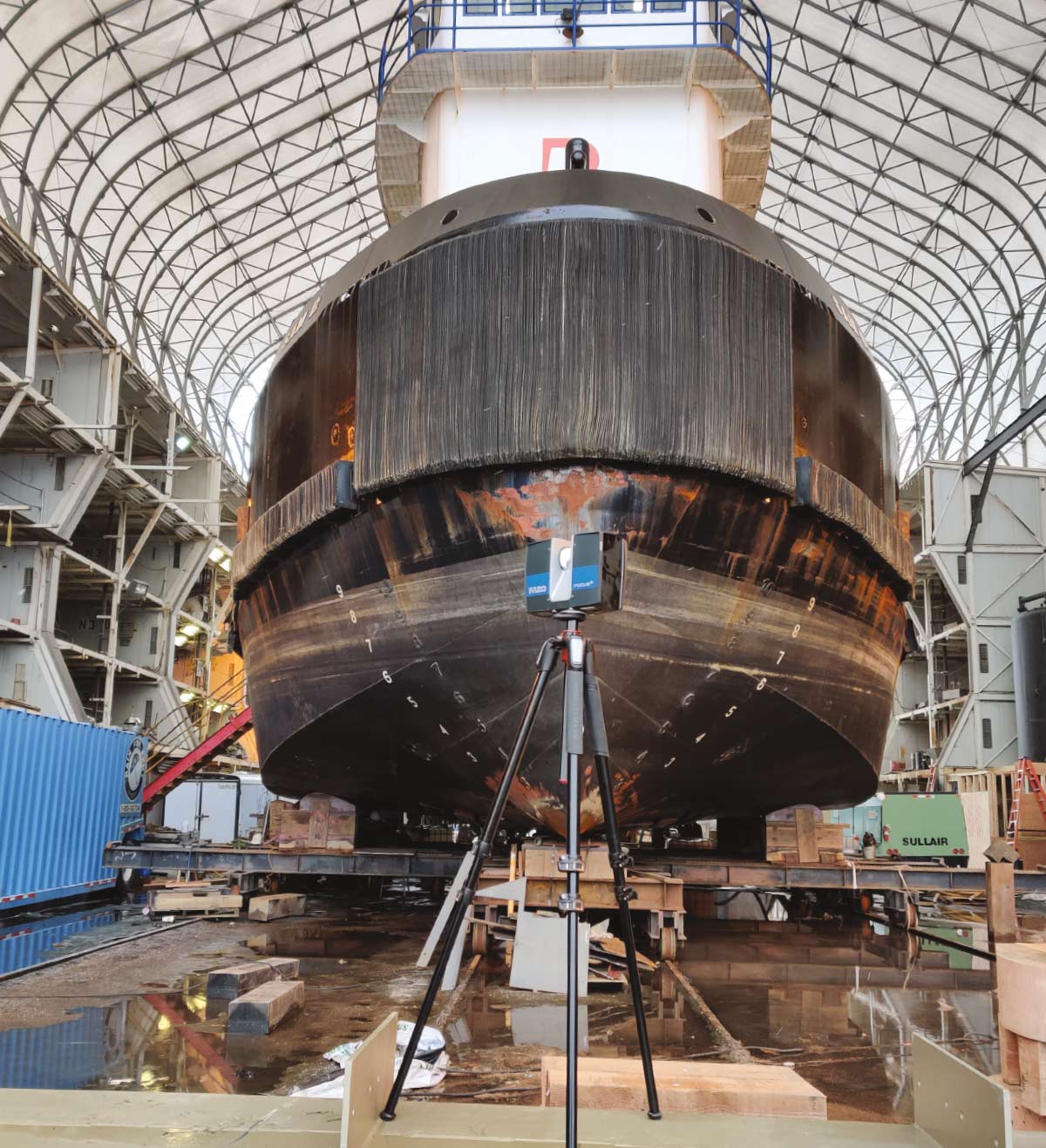
Due to the accuracy of the cut-file, Catalyst Marine Engineering was able to prepare the materials necessary for the modification with minimal waste or manual trimming. This reduced the labor cost, resources, and time needed to complete the project.
Eagle Harbor Engineering
Stillwater Marine Service
Stillwater Marine Service
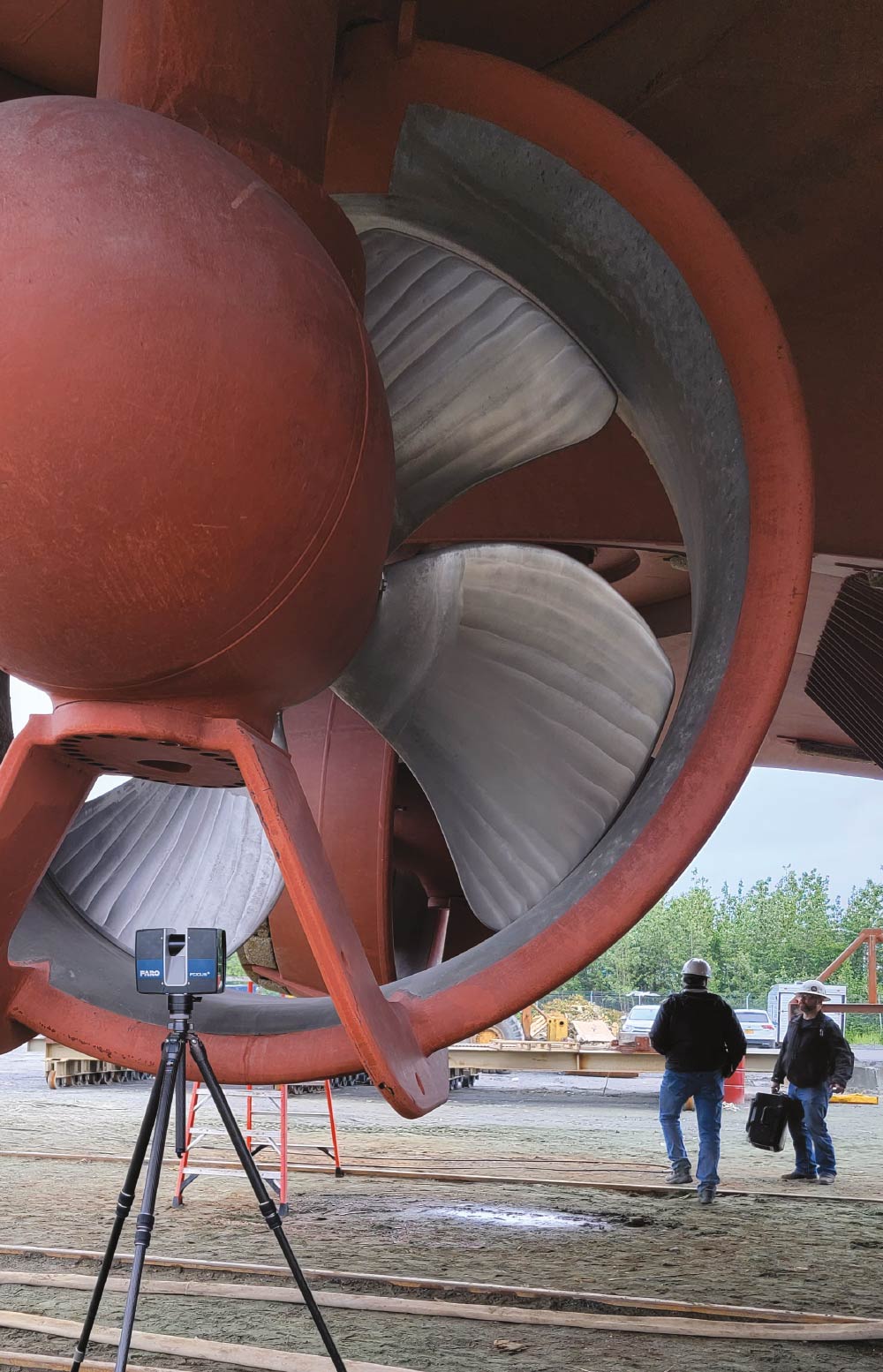
The benefits of the process were not limited to the modifications—it also streamlined regulatory approval through using the American Bureau of Shipping’s (ABS) new 3D model-based class process. Before work began, the modification design was submitted to ABS’ New Orleans Engineering office in an as-built, 3D model format. Once the work was complete, ABS’ Seattle Office surveyed the vessel and approved the modification without issue.
Roy Bleiberg, ABS Vice President of North America Business Development, says: “This was a powerful demonstration of the ABS 3D model-based class process in action. Not only did we deliver efficiencies in plan review and survey without compromising safety but we learned valuable lessons for future applications.”