Big Shovels
ining is the tedious and feverish work of digging precious things out of the ground. Gold mining in Alaska carries with it the sepia-toned nostalgia of 49ers carefully sifting through the infinite waters for tiny flakes of wealth. Those in the industry call this strategy of mining placer mining. And while a few may have made their fortunes that way, both laziness and ambition caused people to search for a more direct path to success. Placer mining is feasible because water flows around and through rock formations with gold veins, slowly eroding the gold and refining it as the water flows downstream. But why not just get the gold directly from the vein?
Lode mining, or hard rock mining, is mining minerals from their very source. As the name implies, hard-rock mining requires a lot more force than letting a stream gently move sediment through settling screens. Even with an army of whistling dwarves to manually chip away at the stone, first one must answer the challenge of getting to the mineral deposit, which is often deep underground. Gold is not the only valuable resource at stake; Alaska mining also produces silver, zinc, lead, and other minerals in smaller quantities. Mining in Alaska has grown to the point that minerals are Alaska’s second largest export commodity.
With the advent of the first steam powered excavator in 1796, people have increasingly abandoned the quaint shovels and pickaxes of ancient times in favor of power. With mineral lodes often having mineral concentrations in the tens of grams per metric ton, substantial work is necessary to remove the valuable minerals from the common rock. The development and refinement of heavy machinery has made lode mining faster, safer, more efficient, and more profitable.
Modern mining in Alaska uses the toughest and most powerful machinery available to drill, lift, carry, and crush more ore-carrying rock than ever before.
Even with access to the strongest earth grinding machines man makes, the sought-after commodity is still buried in the earth, and it’s necessary to get the machines to the minerals. Open pit mining involves positioning the mine directly above the minerals and digging down—removing everything between an operation and the precious minerals. As work on the mine progresses, a pit grows. Alternatively, the plan can be to dig a tunnel through the earth to the material and extract the mineral ores in a more surgical approach.
Open pit mining requires the breaking up, displacement, and removal of massive amounts of earth. The equipment used in this type of mine doesn’t look that unique if seen from a distance. The machines would seem commonplace and fit in perfectly at any commercial construction site: open pit mining uses tracked excavators, front end loaders, and dump trucks just like other earth moving operations. But up close these machines are different—they are huge.
The excavators have a massive reach of up to 73 feet, enough to gobble up a typical single family home in a single bite. Without adjusting their position these excavators can dig a hole 28 feet deep. Powering these machines often requires not one but two engines, each with the ability to generate up to 2,000 horsepower.
The front loaders stand 23 feet tall, almost four Ryan Seacrests in height. With the bucket raised to its maximum height, it towers to more than 35 feet. The bucket can hold as much as 57 cubic yards of material, which is approximately equal to a 10-foot by 24-foot backyard pool.
The dump trucks that are paired with these substantial excavators and loaders are sufficiently endowed to keep pace with the flow of moving earth. A single dump truck can, in a single load, haul as much as 211 tons, which is more than enough to transport more than 450 polar bears in a single trip.
Open pit mining operations don’t simply have one of each of these machines, but often have several excavators, many more front end loaders, and dozens of dump trucks to keep a constant flow of production.
sezer66| iStock
sezer66| iStock
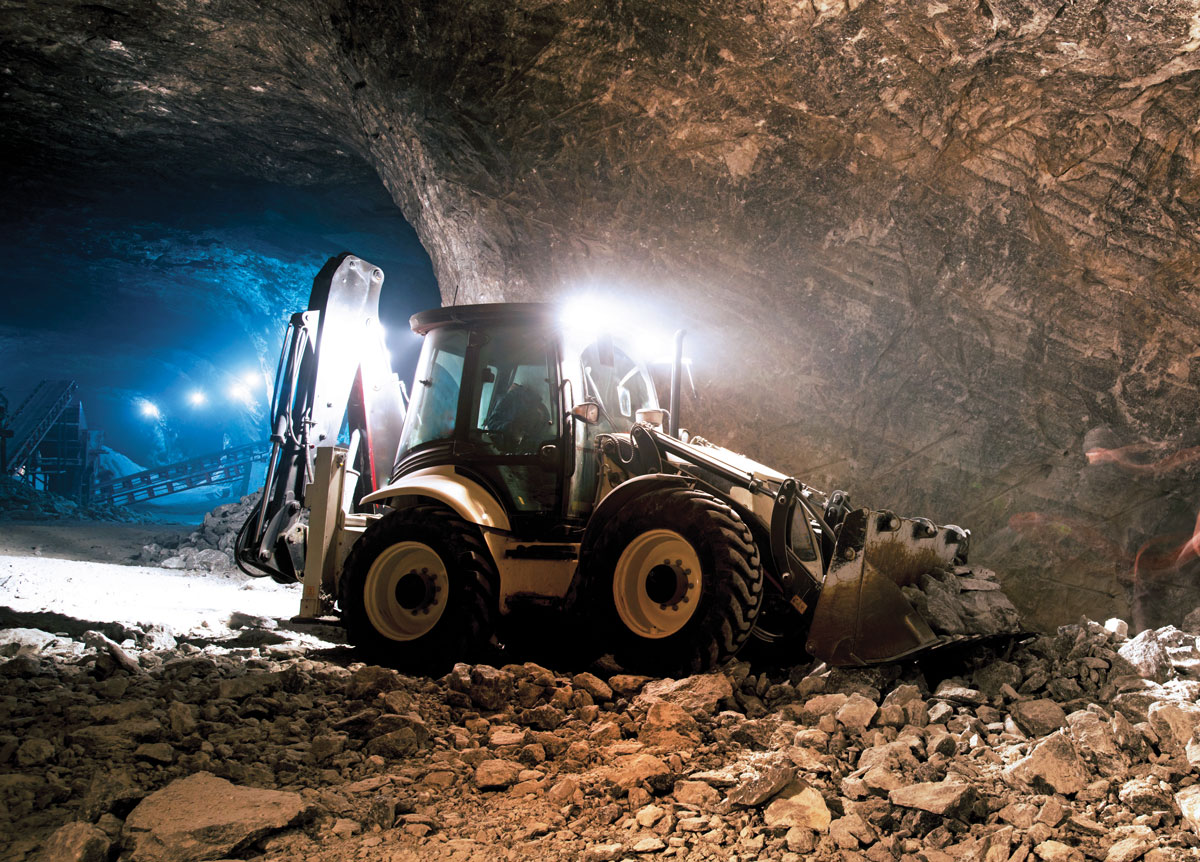
florluca | iStock
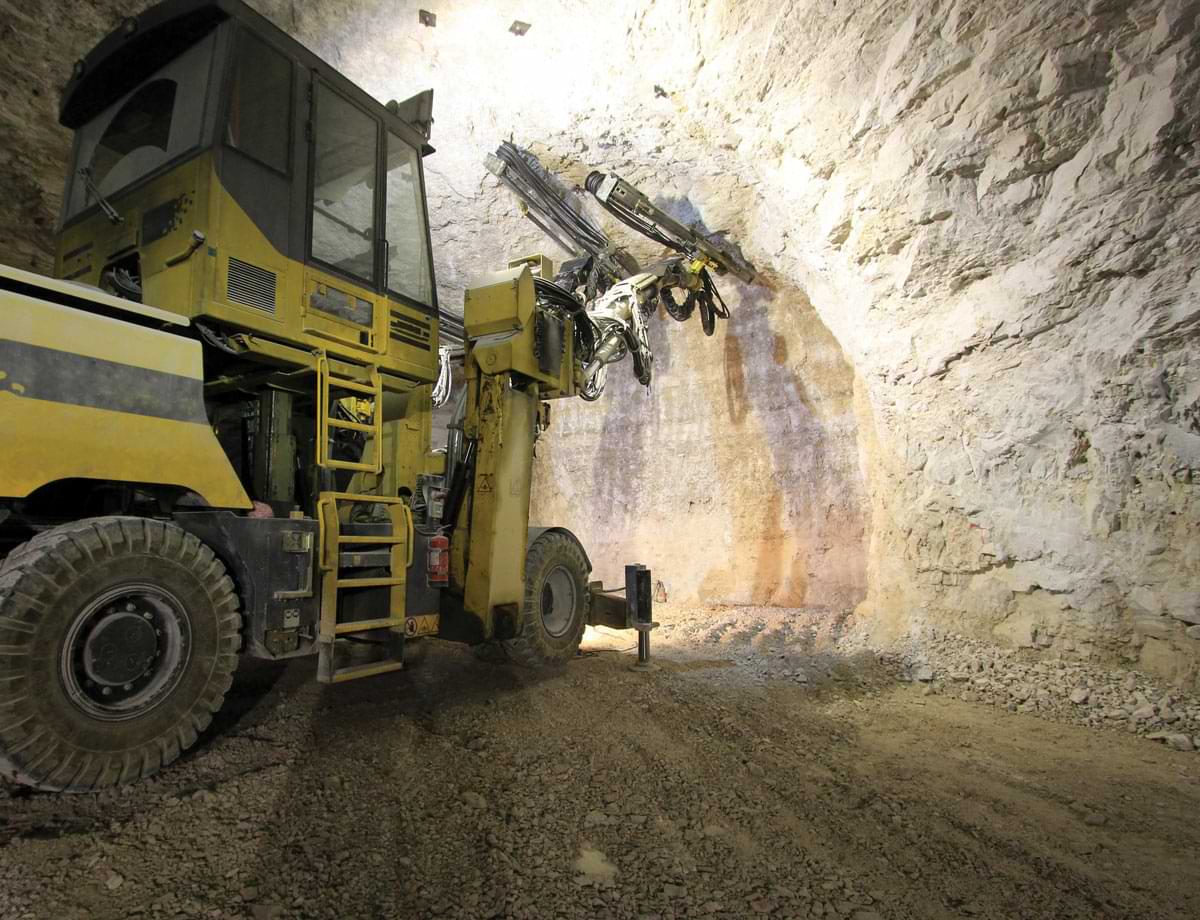
florluca | iStock
The goal of underground mining is the same as open pit mining but must be done within much smaller spaces.
While open pit mining has a front loader as big as a house, underground mining tries to pack strength into a much smaller package. Underground machines also have the unique property of being designed with substantially smaller turning radii than traditional machines so that the equipment can better maneuver in small spaces. These loaders have lift capacities less than a fifth the volume of their open pit counterparts. Underground loaders and dump trucks have a max payload of a “mere” 50 tons.
But underground mining adds drill rigs to the mix of machines. These machines can drill holes as big as 3.5 inches in diameter as much as 90 feet deep. While that is an impressive hole to drill in solid rock, what use could a 3.5 inch hole be when trying to mine vast amounts of minerals?
Underground mining uses machinery: it also uses explosive chemistry. The (in comparison) boring machines are used to create the necessary holes to strategically place explosives, which do the yeoman’s work in breaking up the earth.
And the explosives require their own specialized equipment. Some modern mines use remote detonation systems that allow the operators to detonate the explosives from the surface so that no one is in the mine at the time of detonation. Once the rock and ore are suitably broken up for removal, the loaders and dump trucks move the material above ground for processing.
Dump trucks, drills, and loaders are highly visible mining machinery. But underground mining requires additional heavy machinery that may be harder to see. As holes get deeper beneath the earth, with one cavernous artery connecting off another, human and engine requirements for air are no trivial matter. The fans that push air into the mines have power ratings in the hundreds of horsepower. And with equipment as necessary for safety and operation as ventilation fans, redundancy is required.
With Alaska playing steward to one-third of the US fresh water supply, underground mines must also contend with keeping their machines above water. Water seeps into the mines from various hydrogeologic sources. Managing this problem requires construction of massive wells and the capacity to continuously remove thousands of gallons per minute of water from the mines. Mining equipment used to ensure the safety of the workers is just as impressive and specialized as the equipment used to move the earth out of the mine.
Open structures beneath the earth require support, patching, and sometimes filling in order to ensure the safety of workers and the integrity of the mine. Underground mines operate paste manufacturing equipment, which mixes cement with sediment and materials dug from the mine to produce a hardening mixture. The paste can be used to fill open cavities, reinforce loose or unstable material in the walls and ceilings of the mine or can otherwise be used to patch work already completed.
agnormark | iStock
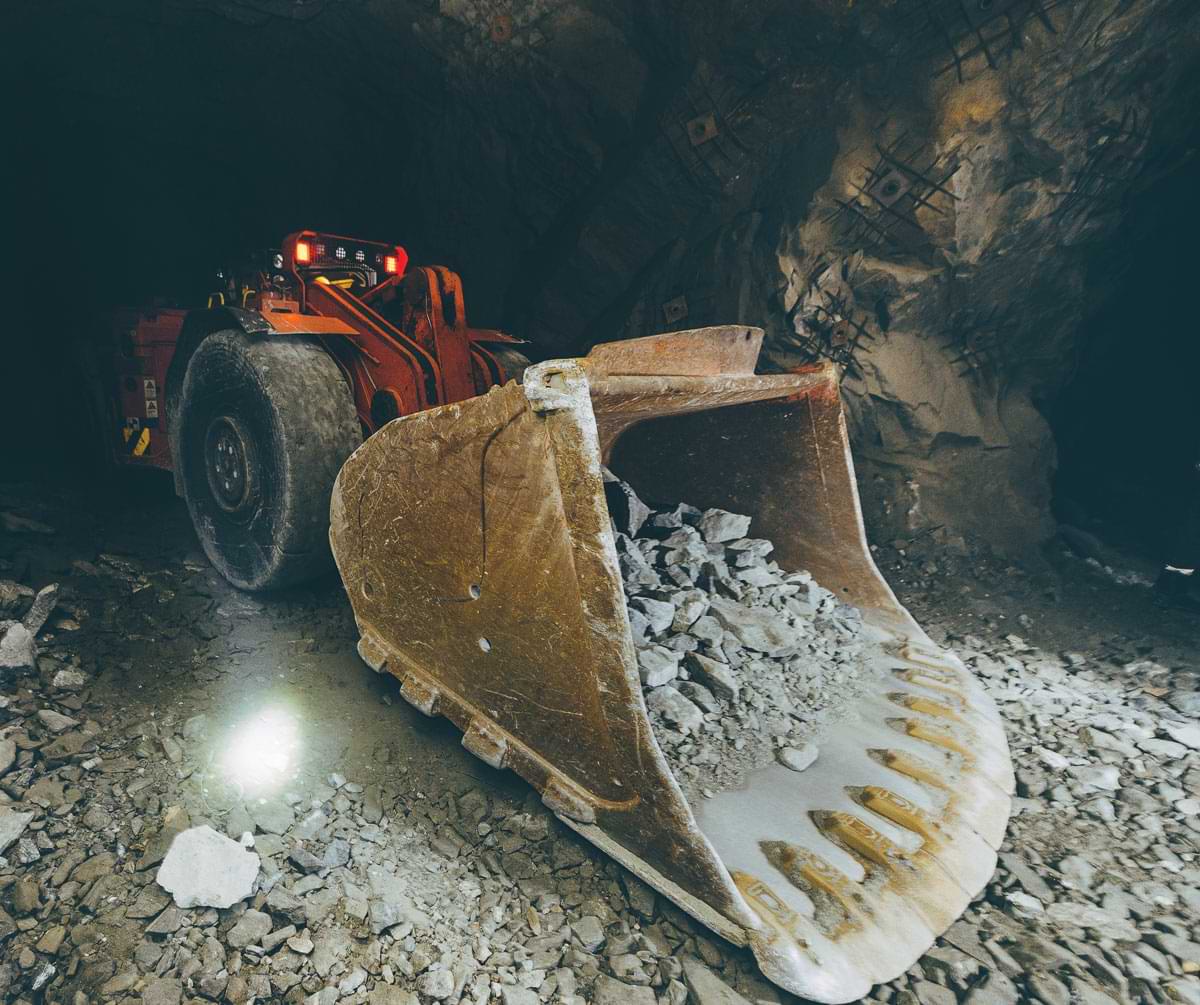
agnormark | iStock
Even after operators extract ore from the open pit or underground mines, the process is just begun. The dump trucks play their critical role moving the rock and ore to the mill. At the mill, the hard rock and ore are fed into grinding and refinement processes to break up the minerals and reduce the size of the pieces of rocks so that the minerals can be extracted. These massive grinders need thousands of horsepower to reduce the size of the rock as necessary for the rest of the chemical and physical extraction processes to be effective. Massive conveyors move the material to the final stages of ore processing. Ore is moved to leech extraction areas to remove the final remnants of the valuable minerals.
For all the specialized equipment and machinery, each piece of equipment requires specialized training to operate. Even routine maintenance requires specialized training, skills, and tools. Imagine the logistical challenges involved in changing a tire on a machine as big as a building with wheels that are taller than the average person and weigh as much as a small sedan. The individuals that operate and maintain the fleet of machines are just as unique as the equipment they operate.
With the quickening march of technology finding new and more exotic uses of materials, commercial and industrial need for raw elements and rare minerals is only likely to increase. And while gold will always be worth removing from the ground, future mining activities in Alaska may include new materials like extracting and producing novel forms of carbon for the next cutting-edge technology. The only question is, what will the right machine be for the job?